ProX four-stroke pistons offer OEM performance and reliability at an affordable price. We dive into how ProX 4-stroke pistons are made and how their high quality is achieved.
In the realm of motocross racing and the ATV marketplace, four-strokes usually receive all the attention. Due to their ease of use, torque advantage and ability to make gobs of horsepower, the valve-and-cam engines have been ruling the roost for the past 15 years or so. ProX has long been involved in the development side of four-stroke technology, mirroring the durability characteristics of OEM/stock piston design, with an eye toward bolstering performance. In fact, ProX uses the same tried-and-true manufacturing plants as several of the OEM suppliers (even making pistons for a few brands). That speaks to the quality that ProX is delivering to customers around the world.
Casting or Forging: The Great Debate
Depending on the application, a ProX piston is either manufactured using a casting or forging process. There are benefits to both. Cast pistons are very stable. The aluminum used is not very sensitive to thermal expansion, so the piston can be installed with less piston-to-wall clearance. This results in a smooth and quiet-running engine. As for a forged piston, this process provides high resistance to impact and fatigue.
Maurice Griffioen, ProX Product Manager, elaborates, “The cast ProX 4-stroke pistons are very reliable replacement pistons for lower performance applications; however, when we’re talking ‘performance,’ the more strong and tough forged pistons are being used.”
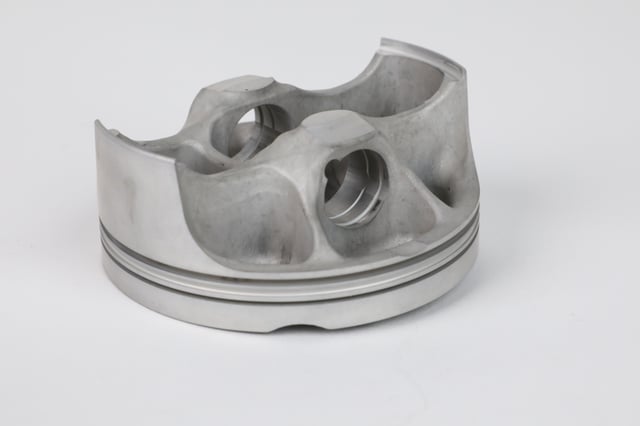
Need some tips on rebuilding your 4-stroke top end? Check this out!
Unlike cast pistons, which are manufactured by pouring liquid alloy into a mold, forged pistons are made by a piece of aluminum being pressed into shape using a large forge press. The forging process offers a stronger piston with an aligned grain flow in the material.
ProX typically uses 4032 series aluminum alloy. Metallurgists will point out that 4032 series alloy is more sensitive to thermal expansion, due to higher silicon content when being cast. However, when this alloy is warmed up gently and in proper fashion, it offers much greater strength with less fatigue. Silicon is needed to improve wear resistance, reduce expansion, and increase hardness and strength. Hardness is key, because it allows for the castings to be machined. Other elements, such as copper, nickel, magnesium and manganese are important. These elements improve hardenability, fluidity for casting, and increase strength at high temperature.
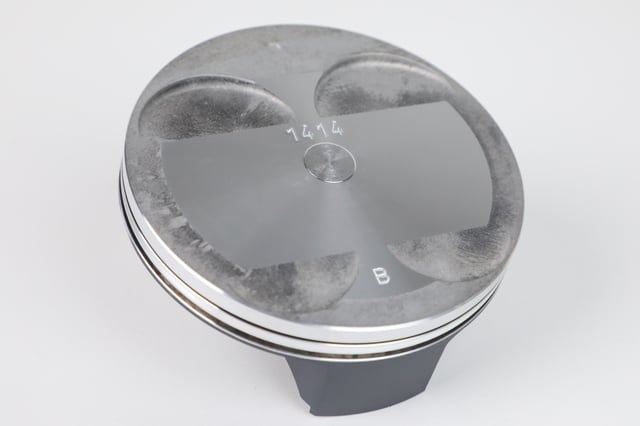
Most ProX pistons contain a 12.5% silicon content. The alloy is called eutectic alloy, meaning that the silicon is combined in a uniform structure throughout the aluminum. Another type of alloy used is a hypereutectic alloy. This hypereutectic alloy has a higher silicon content, which is in the 16-18% range.
Griffioen explains, “The extra silicon results in a slightly harder material that can very well cope with higher temperatures. One of the main benefits is the reduction of ring groove wear. It reduces the chances of micro-welding of the top ring inside the ring groove, which results in less wear and provides very stable oil control.”
ProX’s biggest markets are motocross and the ATV segment. In the cast-versus-forged debate, around 20 percent of ProX pistons in these markets are cast. Forged pistons account for the remaining 80 percent.
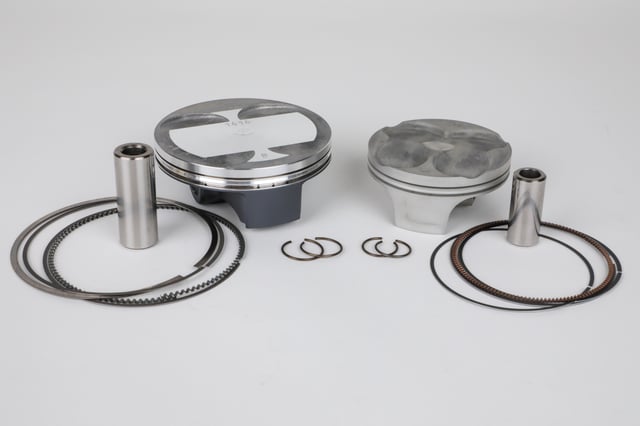
Dedicated Forgings
ProX enlists the services of multiple factories in Japan, as well as the United States, to make their pistons. These state-of-the-art facilities provide the equipment and testing protocols necessary for optimal manufacturing. ProX uses dedicated forgings in higher volume applications. This means that the forging is purely designed for the specific application. This is a spare-no-expense method of piston manufacturing. The juice is worth the squeeze (no pun intended), as dedicated forgings provide optimal strength in every area of the forging. As Griffioen puts it, “This offers the best balance between strength and weight.” Both are important factors in piston performance.
Expanding on dedicated forgings, most of the Japanese forged pistons are manufactured by the “ART” factory, which is the leading piston manufacturing plant for the big four Japanese bike manufacturers.
Griffioen explains, “The quality level and image of the ‘ART’ factory is very high. It perfectly matches with ProX’s image of high focus on quality products. With the pistons being made in the same manufacturing facility using state-of-the-art equipment and premium materials, the quality level is always secure.”

With several hundred different piston models in the ProX range, not all applications are high-volume items. For any of the less popular model applications, ProX can make use of the currently available forging designs in their factory and have the specific pistons machined out of that. This allows them to be relatively flexible in production and make sure to keep the ProX piston range complete.
OEM Replication
ProX four-stroke pistons are made mostly to the OEM/stock configurations, with some part numbers receiving improved features. That didn’t used to be the case. When the modern four-stroke engine was introduced over 20 years ago, forging designs were rather basic. That simplistic approach allowed for significant performance benefits in the redesign stage. However, manufacturers have improved engine power output through improved designs. This has resulted in developing more complex and stronger standard piston forging designs. In fact, box-shaped forgings with struts toward the skirt are becoming standard. ProX four-stroke pistons are crafted following the same tried-and-true guidelines as many OEM/stock designs.
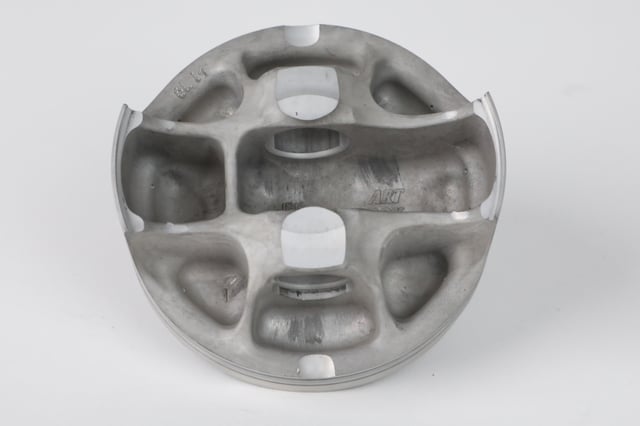
ProX is not just limited to selling products in the aftermarket. Several OEM/stock classified customers make use of ProX’s superior service and great quality products. This involves pistons, as well as other product areas in the ProX range.
With regard to four-stroke pistons, ProX produces pistons for both cast iron cylinder bores and Nikasil cylinder bores. ProX usually offers a large variety of oversizes from standard bore to 2mm oversize cast iron cylinder bores. For the Nikasil cylinder bores, ProX offers a variety of oversizes graded in A/B/C size, each going up 0.01 mm in diameter. With these graded piston size options, the engine can always be set at the optimal piston-to-wall clearance.
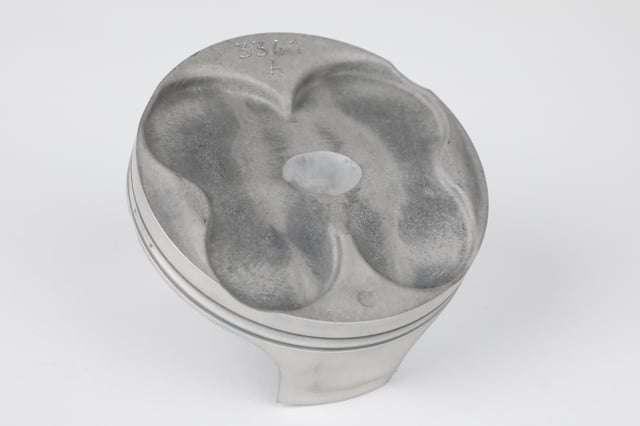
Piston Ring Considerations
ProX pays extremely close attention to the manufacturing of their piston rings. They only use high-quality Japanese RIKEN, TP or NPR rings. In ProX’s decades of experience, they have found that these brands offer the best performing package.
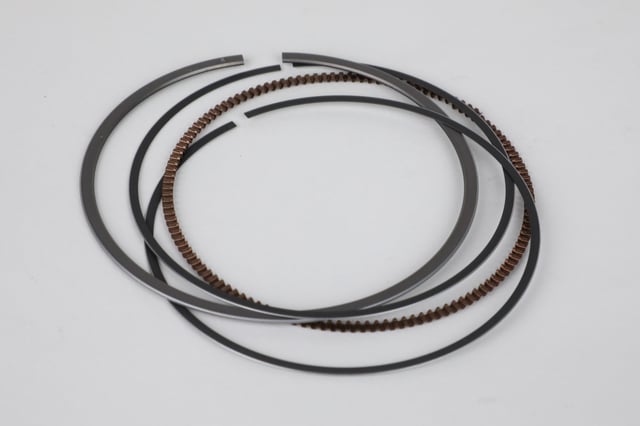
As is the case for most of their piston designs, ProX also typically follows the OEM/stock ring design. However, there are certain instances where ProX will receive special requests from the market to improve on an OEM design. That is because in some cases, the OEM piston has been developed as a single-ring design, but it turns out that the durability is rather poor. To remedy that problem, ProX will opt for a dual-ring design. The extra ring acts as insurance for a positive seal against the cylinder wall, as well as scrapes oil evenly down the cylinder’s cross-hatch, thus increasing the lifespan of the piston. Where a single ring construction may start losing compression sealing ability, the dual-ring design will still hold up.
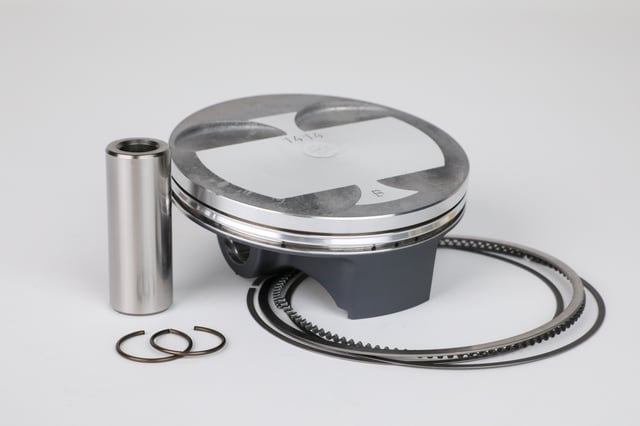